Insulation for Cryogenic and LNG Systems
Cryogenic and below-ambient pipe and tank temperatures can drop to -297°F, making a well-designed insulation system critical to ensure safe and efficient operations in an Liquefied Natural Gas (LNG) facility. We’ve created this LNG resource page to assist you with the details you need to properly design, specify and install insulation systems for your cryogenic and LNG applications.
Below are 7 sections full of resources to learn more about cryogenic and LNG system design, and the benefits of using Trymer® Polyisocyanurate (PIR) insulation:
- The Importance of Insulating Cryogenic Systems
- Designing a Cryogenic Insulation System
- What is Trymer® Polyisocyanurate (PIR) Insulation?
- Benefits of Trymer® Polyisocyanurate (PIR) Insulation
- Installing Trymer® Polyisocyanurate (PIR) Insulation
- On-Demand Webinar: Insulation Systems for LNG Piping
- Additional Resources for Cryogenic Insulation
In an LNG application, if more heat is gained than can be removed by the refrigeration system, there is potential for the system to become pressurized as the LNG vaporizes. Minimizing heat gain is particularly important in cryogenic applications, like LNG, and why a well-designed insulation system is critical to ensuring safe and efficient operations in an LNG facility. Cryogenic and below-ambient piping and tanks should be insulated with a closed-cell foam insulation, and contain a vapor retarder with low permeability.
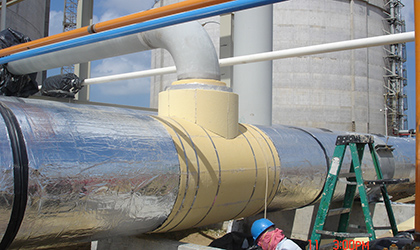
Designing a Cryogenic Insulation System
Minimizing heat gain is particularly important in cryogenic applications, like LNG, so an insulation material that is both thermally efficient and moisture resistant is critical. When specifying a pipe insulation system, it’s important to evaluate all of the variables that contribute to optimum performance and the best long-term value. Connect with a Technical Expert.
Insulation Thermal Conductivity
The thermal conductivity and thickness of an insulation will determine how many layers of insulation are needed to achieve a thermal performance. Trymer PIR insulation products feature excellent (low) thermal conductivity (k-factor) at cryogenic temperatures. Thickness Tables
Insulation Vapor Retarder
Ensuring water and water vapor do not infiltrate a cryogenic system requires a properly installed vapor retarder such as Saranex® CX Vapor Retarder Film & Tape – even with a closed cell material, like Trymer PIR. Learn More
Insulation Compressive Strength
To minimize heat gain into the LNG system, designers prefer to specify insulations with a higher compressive strength, like Trymer PIR to ensure strength and durability to stand up to harsh environments. Learn More
Trymer is a polyisocyanurate (PIR), closed-cell, foam insulation for industrial pipes, tanks, vessels, and equipment used in cryogenic and LNG applications. Trymer PIR can be used on applications that operate at temperatures ranging from -297°F to 300°F (-183°C to 148°C). JM produces Trymer PIR in a variety of densities and compressive strengths to ensure the performance characteristics of the product meet the unique demands of LNG applications. Trymer PIR features a k-factor of 0.19 BTU · in/hr · ft2 · °F at 75°F mean temperature (0.027 W/m · °C at 24°C), one of the lowest ambient k-factors among insulations used in cryogenic applications.
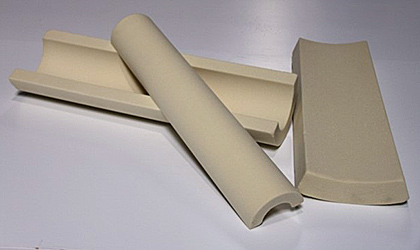
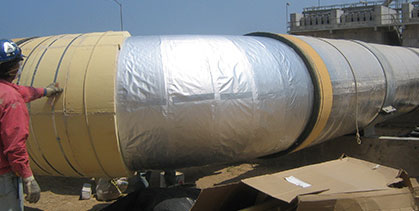
Highly Economical
Trymer PIR is often the most economical choice both in terms of material costs (including insulation, vapor retarder, and jacketing) and installation costs. Learn More
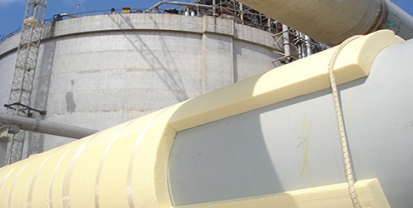
Easy to Fabricate and Install
Trymer PIR is lightweight, easy to fabricate into various shapes, and produced in longer sections (3’ vs. 2’), resulting in fewer joints to seal and less potential for failure. Learn More
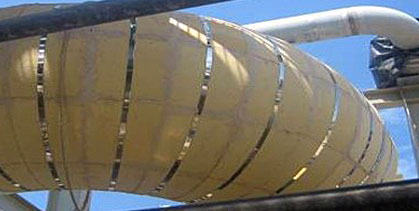
Superior Thermal Performance
By using Trymer PIR, the necessary thermal performance can be achieved in fewer layers (lower total thickness) than the least thermally conductive materials. Learn More
LNG systems create challenges for designers and installers alike. JM's Insulation Intel® webinar explains the following considerations and concludes with a robust Q&A session with our experts:
- Design Criteria: desired service life, environment, and operating conditions
- System Design: joint staggering, contraction joint spacing, supports and more
- Insulation material recommendations
- Overview on installation and system maintenance
Industrial Insulation Intel Blog
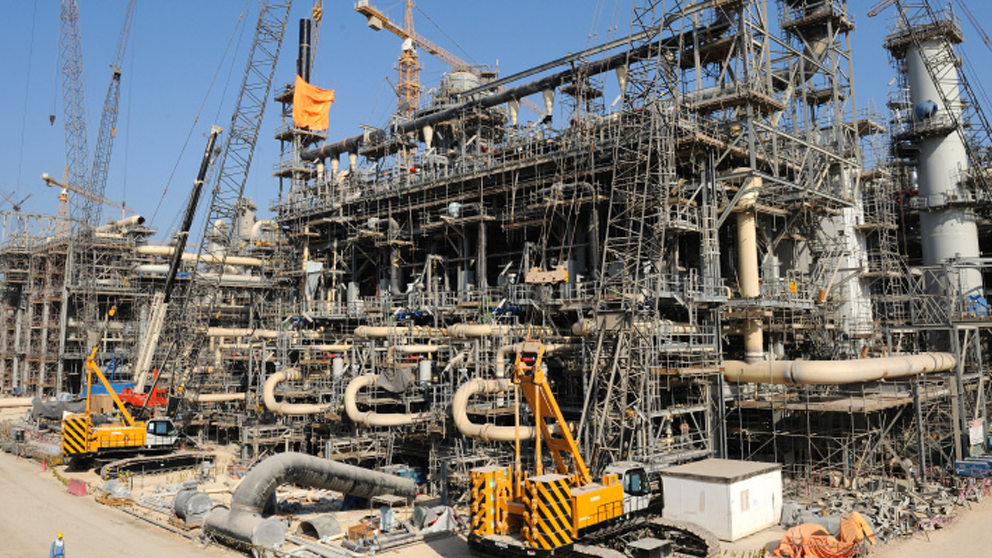
4 Key Characteristics for LNG Pipe Insulation
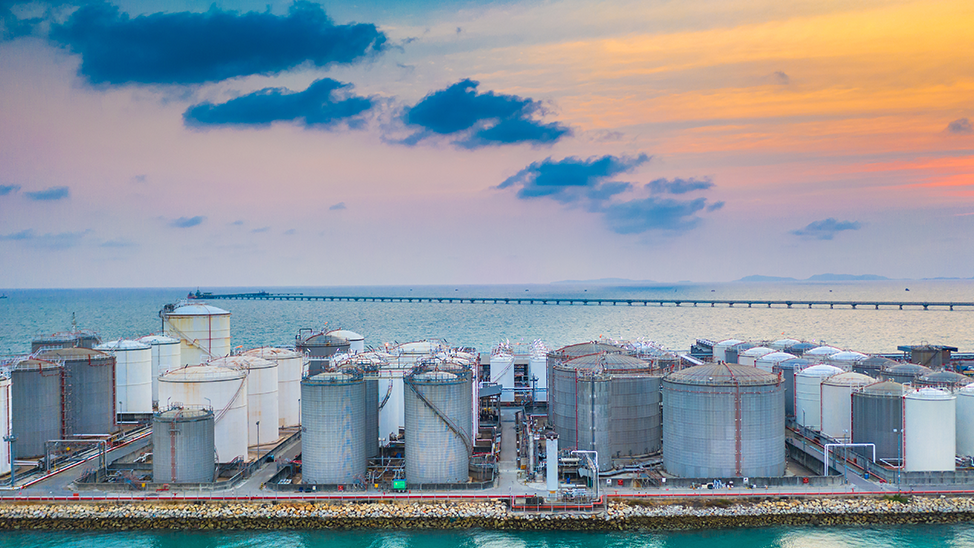