Podcast episode 45 features Johns Manville's new EPDM Product Manager, Kevin Roepe. Kevin discusses Johns Manville's new EPDM FIT Self-Adhered membrane, product highlights, and an overview on the ease of installation.
Above It All is a podcast by Johns Manville dedicated to the roofing industry. The goal of this podcast is to bring knowledge from a Johns Manville perspective on trends, innovations, and people shaping the roofing industry. Join us as we dive head first into enriching conversations about the people and passion that are an integral part of the JM experience.
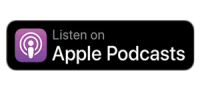
Transcript
Daniel Robbins: Welcome back to another episode of Above It All, a podcast dedicated to the roofing industry by Johns Manville. I am here with one of our new product managers, Kevin Roepe. He is our new EPDM Product Manager and he has some really exciting stuff to talk to us about today. But before we get started, Kevin, how are you doing, sir? Thanks for being on the podcast.
Kevin Roepe: Good afternoon, Daniel. I’m doing great. Thanks for having me, I’m excited to be here.
Daniel Robbins: Before we get into what we wanna talk about, some exciting stuff related to EPDM, tell me about, kind of, what brought you here to JM? What is your background in? And, kind of, what has your journey been like?
Kevin Roepe: Yeah, I’ve spent almost a decade in manufacturing operations, working across a variety of industries, but I’ve always been interested in buildings, architecture, and finding a way to get to the highest point of any city that I ever visited. And so when I found an opportunity to bring me to Johns Manville to take part in their EPDM Roofing Systems, I had to jump on it.
Daniel Robbins: In the past, are you an architect by nature or what is your degree in, I guess?
Kevin Roepe: I have a business degree, but I’ve always been a fan of architecture and design.
Daniel Robbins: Very cool. So I guess the industries you’ve worked in have been geared towards that.
Kevin Roepe: Not at all. The fun thing about manufacturing is that you end up making a lot of interesting products, stuff that you don’t think about everyday, but gets used in your everyday life.
Daniel Robbins: Great experience in manufacturing. I’m sure that’ll come in handy with EPDM because it’s one of the coolest plants I’ve seen yet with a robust manufacturing line. Have you been there yet?
Kevin Roepe: No, I have not. I’m flying out on Monday to check it out.
Daniel Robbins: Very exciting. Well, with that, let’s move on to some of the cool, exciting stuff related to EPDM SA. Can you go ahead and just tell us a little bit about that product? Then, let’s talk about the content that we have available for contractors. [Also,] what are some value propositions with it?
Kevin Roepe: Yeah, certainly. So we have a new EPDM FIT Self-Adhered membrane that we’re introducing to the market October
1st. This is an exciting expansion to our EPDM portfolio that offers up to 3x faster installation compared to traditionally adhered EPDM systems, and it offers an extended window of installation thanks to a temperature range of 20 degrees and rising. This provides increased benefits in our colder climates where traditional adhesives have a longer flash-off time, and it takes more time to install an EPDM system.
Daniel Robbins: That’s very cool, let’s talk about that. I’m sure some of you contractors and some of you listeners understand, selfadhered products, they go down fast. Three times faster, up to three times faster, is an important statement because I think that goes in alignment with the elimination of traditional adhesives. You know, before you’re having to roll out the adhesive, and then maybe let it flash a certain way, and then put the membrane out. Here, you’re just kicking out the roll, you’re peeling the release liner, you’re brooming it, and then you’re using a weighted roller afterwards?
Kevin Roepe: Yeah, a split-steel roller to really promote that adhesion. But you bring up a good point. We’re not relying on traditional adhesives, the adhesive is already installed on the roll. We’re offering labor and time savings by not needing to load pallets of adhesive onto the roof. We’re saving time by not having to fold back the membrane, roll or spray on adhesive, wait for up to 30 minutes for it to flash off, and then we’re also reducing job site waste because we’re not loading all these subsequent canisters of adhesives and packaging up onto the roof. So we’re eliminating the amount of stuff that the crew needs to move up and down, and the amount of waste you need to handle on the back end of a project.
Daniel Robbins: That is huge. I know a lot of customers will really appreciate that. Let’s talk about the product a little bit. I know it comes with a split release liner, and in the field, I know that can come in handy and give us various install methods. Let’s just kind of touch on those lightly so that people understand, like, it’s not one way to do this. You kind of got two ways to do this, and it gives you, I think, the ability to work in tighter spaces on the roof if you need to use one method over the other.
Kevin Roepe: Yeah, so the product, this new product has a split release liner covering the factory applied adhesive on the back. The
liner is split down the middle, across the length of the membrane. The membrane also has a three inch strip of factory in-seam tape on the edge; the same factory in-seam tape that we’ve used on EPDM products historically that provides superior seam quality, additional labor savings by not having to prime tape. To your point, yes, there are multiple installation methods that you can use. One, targeted more towards large open sections of the roof where the crew has a lot of area to work, where you can get a operator on each side of the membrane, peeling the liner out from underneath, and adhering it in large swatches. Alternatively, we can demonstrate another installation method where you fold the membrane along the vertical length, and then you can peel out the membrane from one, the release liner from the membrane on one side, adhering it to the section of roof, and then folding it down to adhere the other side. That is great in areas where you have obstructions like pipes, vents, HVAC units, if you’re up against a parapet wall. So areas where you are a little more space constrained, we offer that dual installation ability.
Daniel Robbins: Yeah, I saw that. I was able to go up on the roof with one of our customers who was using the product, and that fold over method, the second method that you talked about, I noticed them really utilizing it when [they] had penetrations on the roof. They would be able to have the one side that’s folded over, cut appropriately, to then fit around the penetration when they would fold that part over. Then of course, use, I believe it was, it’s our seam strip to seal that in.
Kevin Roepe: Yeah, anywhere where you would cut the membrane to go around a pipe or penetration, you would then use our six inch peel and stick sealing strip, to strip in the seam.
Daniel Robbins: That’s perfect. So let’s talk about, we’ve actually really, I feel like we’ve done a great job, kind of, creating content around this because we want everyone to be able to install it properly. We want everyone to have all the right details and everything. [Tell] us about the gamut of stuff that we have, tools wise, for customers and in JM employees alike to learn more about this product.
Kevin Roepe: Yeah. We have a broad variety of educational content available on our website, including installation guides, and
installation videos that demonstrate both of the installation methods that we talked about, as well as touching on some of the common side lap and end lap details that you would [use] in an EPDM membrane installation. We also have a self-adhered sample kit that includes a benefits guide that highlights all of our product features, as well as providing multiple samples of the product. So you can actually get a feel for it, peel the release liner, see how it handles without having to operate a full roll.
Daniel Robbins: I love that. People can get their hands on it and kind of just see what it’s all about before they just go ahead and buy a bunch of pallets of it.
Kevin Roepe: Exactly.
Daniel Robbins: I dig it. I dig it. Well, that about wraps time up. Thank you so much for enlightening us on this new product. I’m excited for contractors to start using it because I know it’s gonna be a huge benefit to whatever their process has been using traditional adhesives.
Kevin Roepe: We’re certainly excited to be introducing this to the market and look forward to seeing more get rolled out across roofs nationwide.
Daniel Robbins: All right. That wraps the podcast. Everyone stay safe out there and we’ll catch you next time. Bye.