Above It All podcast episode #28 features Research Manager, JR Babineau, for Johns Manville Commercial Roofing. Join us as we discuss the importance of continuous insulation when designing buildings, what it means, and why we innovate products the way we do.
Above It All is a podcast by Johns Manville dedicated to the roofing industry. The goal of this podcast is to bring knowledge from a Johns Manville perspective on trends, innovations, and people shaping the roofing industry. Join us as we dive head first into enriching conversations about the people and passion that are an integral part of the JM experience.
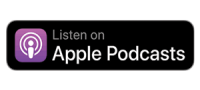
Transcript
Daniel Robbins: Okay, I’m gonna kick us off. So here we are again for another episode of Above It All, a podcast dedicated to the roofing industry by Johns Manville. Today Francis Babineau is gonna be on, and he’s been on before, he is a huge technical resource at the company, he knows the ins and outs of all of our products that the company offers, but also roofing. And so he did this presentation on continuous insulation recently that I felt like it really does answer the why, and so I was hoping he’s gonna dive in and kinda give us a short answer to that very long 50-minute presentation so that everyone can take something away that’s really valuable about why we develop the products that we develop, and what our end goal is for developing those products. So with that, Francis, how are you, sir? Thanks for being on the podcast.
Francis Babineau: I’m great, Daniel, thanks very much for having me on again.
Daniel Robbins: So that presentation you did was great, as I said before, to our listeners, it’s very, very long and we’ll have it on our website, so eventually everyone can get to it if they really wanna download something that goes very, very in-depth in this topic. But today’s topic is gonna be about continuous insulation and thermal bridging and problems related to all of it, answering the why of why we make our products. So with that, can you tell us what continuous insulation means to you and tell me the importance of it.
Francis Babineau: Sure, and you’re right, the webinar goes into it in a lot of detail, but at its core, continuous insulation is kind of really just as the name implies, it’s insulation that is continuous across the entire building envelope without any sort of breaks or interruptions, ideally even without metal fasteners going through it. I’m actually, I’m a big fan of adhered roofing systems or the fasten one adhere one strategy as well, because these things really let us deliver truly continuous insulation performance to the roof, and even when we look at walls, there’s ways to do it on the walls as well, usually not by adhering them, but other ways.
Daniel Robbins: So that adhered technology that you’re talking about in combination with the fastener element, so why not do all fasteners? Well, let’s dive a little bit more then, I think probably the term for that is gonna be related to thermal bridging, correct?
Francis Babineau: Yeah. At least, that’s certainly one of the big reasons. The metal fasteners, they do an awesome job, I’m not opposed to all-fasteners, they do an awesome job to hold things down to really take and collect loads like from wind and other things to... That get exerted onto the roof, and we need to transfer that back to the structure to hold everything together. And so fasteners are important for that, but they are usually steel, and steel is a fantastic conductor of heat. So I’m really a big fan of this kind of, of the strategy of maybe the first layer of insulation gets fastened down and then everything above that gets held down with adhesives because then that really lets us get the best of both worlds out of that scenario. We get the mechanical strength of the fasteners, but we don’t get the penalty, the thermal bridging penalty that we would have if we had fasteners going all the way up to secure the membrane down.
Daniel Robbins: Very cool, and I know there’s a few different types of thermal bridging. Do you mind kind of lightly explaining about what those are and how they’re relevant?
Francis Babineau: Sure, sure. So like we talked about in the webinar too, there’s a lot of different thermal bridges, but it’s essentially anything that let’s heat flow around the insulation, ideally we want the insulation to be in the way of any heat moving into or out of our building. So in commercial buildings, steel and concrete are the most common materials because that’s what we build out of, they’re strong and they’re durable. Specifically looking at roofs, thermal bridges related to the roof usually are some sort of framing, or it could be the roof deck itself especially at the parapet where we’re connecting the roof to the wall. Thermal bridges could also be things like pipes and duct work or other sort of mechanical penetrations, and like we’ve already talked about, even fasteners and plates can cause thermal bridging, if there are enough of them. The impact to the insulation performance, it’s really gonna vary, it depends on the material, how much of it there is, how many thermal bridges there are, what climate the building’s in, all these things come into play and interact to say, “Oh, this is really bad,” or maybe a certain scenario isn’t quite as bad.
Daniel Robbins: So to make sure I understand this correct, there are always thermal bridges on a construction, but the point would be to mitigate how the heat travels through those bridges, correct?
Francis Babineau: Absolutely correct.
Daniel Robbins: That’s very cool. See, I’m just now diving into really understanding what that is, and the way that you explain it was perfect, the reason that contractors are building their structure a certain way is really to insulate the inside of the building in every form and fashion. It’s not just like the roofing system, it’s like as you said, the concrete, and it’s the wood frame and it’s everything. And so that kinda leads to this next question, let’s talk about heat loss and how a contractor or architect is going to calculate how to properly insulate their project. And is that really an architect who’s doing all that work or is that a contractor? Francis Babineau: So the calculation side is gonna be usually some sort of design professional. It could be the architect or somebody in the architect’s office. It could be somebody from the mechanical engineering firm. Oftentimes, those guys are in charge of sizing the heating and cooling system, and so calculating this stuff correctly is really important to them or sometimes there might be an energy consultant brought on. So their job might be, again, to make these calculations and then maybe run an energy model of the building to show energy code compliance or to go after some sort of green certification.
Francis Babineau: So the design professional is usually doing the calculation side. And then of course, the way we build buildings, the hand-off to the contractors to then say, “Okay, now I’ve done these calculations and made these drawings, now go build it in the real world and make it all work.” And so it’s important on both sides, because oftentimes, the smallest of details don’t really show up in the drawings. They’re just kind of assumed as good practice, and that’s where the skill of the contractor comes in. Sometimes they may specify things like adhere one, or fasten one adhere one or fully adhered where those things might get specified. The details of how to do it really falls to the contractor.
Daniel Robbins: Fascinating. And so those values that they’re working with are typically that U-value and the R-value in relationship to the whole structure and every part of the structure. Correct?
Francis Babineau: Yes. So just to kind of give a little bit of detail without going down the rabbit hole too much, R-values really are... R-values go with materials. So for example, our ENRGY 3® Polyiso product has R-values associated with it, depending on its thickness. Same thing with our cover boards, our... Kind of recall now, the SeparatoR®, ProtectoR®, Invinsa®.
Daniel Robbins: We have ProtectoR HD.
Francis Babineau: Retro-Fit™ board, all of those cover boards. They all actually have an R-value associated with them. But then the U-factor, that’s what we associate with the whole assembly. And so that’s the number that will include thermal bridges. So most commonly in the energy code today in the US, we really only care about framing. So for most low slope roofs that are maybe some sort of steel frame with a metal deck, and we put Polyiso on top of the deck. That becomes kind of easy because we’ve eliminated the thermal bridging. But if we take an example like maybe of a wood deck in California, for example, where we might see a wood deck with either steel or wood rafters or joists to support that wood deck, lots of times, not all the times, but sometimes those get insulated from the bottom. So instead of Polyiso on top, which is what we would prefer, they get like fiber glass or something else to insulate those roots from the bottom just between the framing.
Francis Babineau: And so in that scenario, then we actually need to account for the heat that’s gonna flow through those rafters or joists in addition to the heat that flows through the cavities. And that’s when it kinda dumps back over to the architect, to the mechanical engineer to do those calculations. And the simplest way to think of it is that U-factor is just one over the R-value, so the math is not necessarily complicated. And then it works the other way too, to get back to R-value, we just take one over the U-factor. Just to give a sense of how that works when we have to actually...
Daniel Robbins: Well, it’s very... Oh sorry.
Francis Babineau: I don’t know how far in do you want to go. [laughter]
Daniel Robbins: No, go a little bit further this is honestly, so enlightening, and I know that a lot of listeners will appreciate it. So keep going, this is awesome.
Francis Babineau: Okay, so when we actually need to calculate a U-factor, like in this example of, let’s say, a rafter roof in California, where we’ve insulated from the bottom, we actually break the roof up into these what we call paths. We take a framing path, basically a slice through the roof at one of the joists, and we look at all the layers in that particular path. So we’re gonna have the membrane, it may be a cover board, the roof deck, and let’s say the framing, whatever that is, well, let’s say it’s like a big 2 x 10 wood rafter. And then we take a similar slice in the cavity. So in the cavity slice, of course, then we’ve got membrane, maybe a cover board roof deck and now the insulation. So we... All of those different materials have an R-value associated with them. As you can imagine for something like the membrane, that number is very small, but we add all those values up and we get this overall R-value for all of these layers for each of the paths. And then that added up overall R-value for each of those paths we do the math, take one over that to get a U-factor. And then once we have U-factors, then we basically take an average, an area-weighted average.
Francis Babineau: So if that roof maybe has 15% of the total area of that roof is taken up with framing, we would take 15% times the U-factor for that path plus 85% times the U-factor of the other, add that all up. And that gives us our overall U-factor for the whole roof, and then now the mechanical engineers stop there ‘cause that’s the number that they care about. For code compliance or just for most of us to intuitively get a sense of, how good is this roof? Then we take that overall U-factor, do the math again, do one over that to get an overall R-value for the whole assembly, and that gives us a sense of, is this roof good or is thermal bridging really hurting us? So in the example, let’s say we put R30 fiberglass batts underneath that deck with wood framing, when we do the math, that ends up being only about R27 overall, so the wood framing hurts us a little, but not too much.
Francis Babineau: If we were to take that same roof, but throw steel joists under there instead of wood, that R30 becomes just R24, so a much more significant hit, which is again why from Johns Manville’s perspective, we really advocate for insulation above the deck because then it’s continuous, we don’t have to worry about degrading the performance by thermal bridging through framing or other paths.
Daniel Robbins: That is very cool. So really to simplify things, you’re looking or the mechanical engineers or whoever is trying to meet the building code is looking for that average. And then also looking for materials in that average that could either be switched out or mitigated somehow to help bring a stronger R-value overall.
Francis Babineau: Yes, yes, exactly right.
Daniel Robbins: That is very cool, and I know that’s a lot for people to hear. So at the same time, I do encourage people to go check out the webinar if they wanna get greater details, ‘cause he’ll have all the charts up about how you’re calculating all this stuff and it really makes sense when you do look at it, it’s very simplified the way that you did it, JR, so I applaud you for that. Moving on to that health and safety perspective, let’s talk about CI from that perspective, and then its relation to occupant comfort and interior air quality.
Francis Babineau: Sure, yeah, no problem. The question tees it up nicely, thermal bridging, we kind of tend to focus on it, design professionals from an energy code, energy perspective, we need to address it if we’re gonna meet the energy code. Okay, fine. But the reality is, is that there’s a lot of other impacts, thermal bridges just all across the building enclosure can cause a lot of problems in CI, Continuous Insulation is really important to help address that. Effectively installed, Continuous Insulation can eliminate cold spots that can occur in corners around windows and can even help eliminate cold floors, which can happen when you have like an exposed edge of a floor slab. All of these factors can really directly impact occupant comfort, especially imagine like a multi-family building, so a high-rise apartment or condo building, it’s probably gonna have poured concrete floors, sometimes they extend those floor slabs out as part of a balcony, that becomes a big... That’s a big sin, basically. It’s taking the heat from inside the building and really cheerfully rejecting it to the outside whenever it gets a chance.
Francis Babineau: But if we design the building differently, if we wrap the edge of that slab with Continuous Insulation, use something else to create the balcony. We can eliminate a lot of these cold spots and from an indoor air quality perspective, eliminating these cold spots with CI really reduces the risk of condensation. And so that’s important because condensation, thermal bridges located, I should say, in places like closets or behind furniture that can lead to condensation, that can even lead to mold and mildew. But if we can again, use Continuous Insulation to eliminate these, we eliminate those hazards and ultimately we make an even more robust and durable building enclosure. So roofs and walls, all of it benefits from Continuous Insulation.
Daniel Robbins: It sounds like that mold thing has always been... I’ve always heard that being a key issue with a poorly designed building. Is that something common that you come across or is it just one element that CI can help tackle?
Francis Babineau: I mean, yeah, gosh to say we come across it a lot, I don’t know a lot, ‘cause there’s a lot of buildings out there, they’re not all failing. But it’s definitely an issue. Cold spots leading to condensation, absolutely can lead to issues, and part of it just depends a bit on the building, multi-family buildings, things like that are usually not so hot and humid, but imagine something like a rec center with an indoor pool. And we take that rec center and let’s go build it up in the mountains in Breckenridge or Avon here in Colorado, well, suddenly now that’s a big deal, and it becomes even more important that we manage that and that we design that building enclosure well, so that there’s not any random pieces of concrete or steel that are cold because they are a thermal bridge that are now exposed to this hot, humid environment. So certain buildings require a lot more care than others, I would say.
Daniel Robbins: Sure. Based on climate, location. That is very cool. So it sounds like you’re juggling a lot of factors when you’re designing products on a regular basis.
Francis Babineau: Well, yeah, you’re right. But yeah, products, certainly, and also just how they’re used, and I would say that’s an important part of... What we do at JM is we need to not only make products that work, we need to really understand how they’re gonna be used in the building. So that they get used right and they do the job we want them to, frankly, so they don’t get misused ‘cause that can happen too.
Daniel Robbins: Now, at the end of these projects, is the R-value and the U-value, are those recalculated to do a new assessment of what’s been built and how it worked out or is it kind of like once the original code is met, everybody goes on their way and then they wrap the production, so to speak.
Francis Babineau: I would say it’s really bad, I would say today, there’s not a lot of going back and re-calculating things, unless... I would say the only time that I know that something gets re-calculated is because there was a change done kind of all on the fly, some sort of change order occurred. So the original design is not what was built and then those calculations probably need to get redone, if nothing else, just to demonstrate that the change is still compliant with the energy code.
Daniel Robbins: Sure, and then lastly, I guess as an innovative brand that JM is, you’re constantly trying to push the envelope with creating products that have a higher R-value, but maybe are lighter in weight or have other really cool benefits that can be huge for people working on the roof with them, and then ultimately even in application throughout the lifetime of the building.
Francis Babineau: That’s exactly right. That’s definitely something that we are always working on here at JM, both in the roofing division and also in R&D. We’re always trying to push things along and get... Have products that are better R-value, oftentimes products that will bundle together, different functions. So you can get good R-value and good, say like protection for the roof, any time we can start bundling these functions together, it usually ends up being a win when it comes out to the job site.
Daniel Robbins: Sure, ‘cause you can only get so much out of a membrane. So you’re talking about the importance of figuring out the right bundle to an application.
Francis Babineau: Absolutely, yeah, that’s really key. We’ve got... We make a lot of... JM and roofing in particular, we make a lot of different products, and so there’s a lot of combinations and really understanding what are the best, what are the optimized combinations for a given scenario. That’s really a key part of what we do.
Daniel Robbins: Yes, and we encourage all contractors listening to this, to consult your local tech rep or JM representative on the right bundle for your project. But with that, we are out of time, JR, thank you so much for enlightening us, and we hope to have you again on the podcast.
Francis Babineau: You’re so welcome, Daniel, I really appreciate it. Good chatting with you.
Daniel Robbins: Alright, thanks.
Daniel Robbins: That is the podcast. Thanks so much for joining us on this episode. And like I said, we will be providing a link in the description that will be on our podcast page, which will be on our blog, which will go to the 50-minute long presentation, if someone wants to get a more in-depth look into this conversation, ‘cause it really is, it’s really valuable to know. I’m sure there’s a lot of contractors and building designers out there that knew about this, but we’re all catching up. You can subscribe to all episodes on Apple Podcast, or of course go to our blog on our website, and all of the episodes are there as well. Stay safe out there, and we’ll catch you all for the next episode. Thanks, bye.