We recently published Part 1 of the blog series,Don’t Settle When It Comes to Vibration. The previous blog addressed several types of insulation that you can use in high-temperature industrial applications where vibration is a component of the environment.
As discussed previously, the temperature of the application plays a critical role in establishing whether or not the insulation will be able to perform in such a physically demanding application. Specifically, when the application operates at temperatures that exceed 600°F, we have observed mineral wool beginning to fail at a structural level because of binder burnout. The data show the binder utilized in most industrial mineral wool insulations will begin to oxidize at temperatures at and above 600°F, causing the material to lose its compressive strength and, subsequently, sacrificing its structural integrity. Under these circumstances, mineral wool can sag, settle, or compress, compromising the thermal performance of the insulation. This is where the other materials, like calcium silicate and InsulThin™ HT, a microporous blanket, should be used.
Calcium silicate products don’t sag, settle or compress at temperatures over 600°F because they are molded, mineral-based insulations. InsulThin HT’s material makeup, however, is entirely different – it is a quilted, flexible, microporous blanket. InsulThin HT offers higher compressive resistance than mineral wool, while providing better thermal performance at elevated temperatures than many other traditional high-temperature industrial insulations (including mineral wool, calcium silicate, and high-temperature silica aerogel industrial insulations). However, since it is not a molded, mineral-based insulation, it’s natural to wonder whether or not InsulThin HT experiences a high-temperature burn off similar to mineral wool, which could subsequently lead to compression, sagging, or settling at high temperatures
The microporous blanket is made of fumed silica particles intertwined with glass reinforcement fibers to form a composite material. The mixture of fiber and fumed silica is layered between two sections of cloth and sewn together with a thread, providing a quilted look. While the fumed silica particles and glass reinforcement fibers do not oxidize within the insulation’s operating temperatures, the thread may begin to degrade at temperatures starting at 600°F; however, unlike the binder in mineral wool, the threads are not a critical component of the material’s structural integrity.
While there is no specific ASTM test method to evaluate insulation settling due to vibration, we have explored InsulThin HT’s ability to maintain its structural integrity, without the thread, in environments that experience excessive vibration, by designing our own test method based on ASTM C411Standard Test Method for Hot-Surface Performance of High-Temperature Thermal Insulation1.
ASTM C411 measures the sag-resistance of pipe insulation due to high temperatures and has a passing criteria threshold of + 5% of the original insulation thickness. We based our testing on a modified version of ASTM C411, with an added element of vibration, for a duration of 100 hours. The objective of the test was to explore whether InsulThin HT experiences sagging, settling, or deformation in applications where the levels of vibration are considerable and the stitching is no longer present.
For the test, we installed two, 10mm layers of the microporous blanket on an 8” pipe section and jacketed the insulation with stucco embossed aluminum jacketing. The assembly was then conditioned at 600°F for 24 hours, the temperature at which the stitching begins to degrade.
At that point, the thickness of the insulation between the jacketing and the pipe was measured using calipers.
Measurements were taken at the top and bottom of the assembly. The assembly was then clamped to a
metal table where a vibration device was attached that would vibrate the insulation assembly for 100 hours.
Throughout the test and upon its completion, the top and bottom insulation thicknesses were measured on an
average of every 3 hours (36 measurements over the course of the test) to determine whether the vibration
caused any settling within the assembly.
The results showed that even after 100 hours of constant vibration, the microporous product did not settle or
compress. The insulation retained its shape and relatively uniform thickness despite the comparative absence
of the thread used to hold the fiberglass cloth together. The insulation thickness demonstrated a +1.5% deviation
from the average thickness that can be attributed to measurement variability due to the vibrational component
of the test. Graph 6 below shows the relatively limited variation in the material’s thickness, ranging between
21.7mm (maximum thickness) and 21.1mm (minimum thickness).
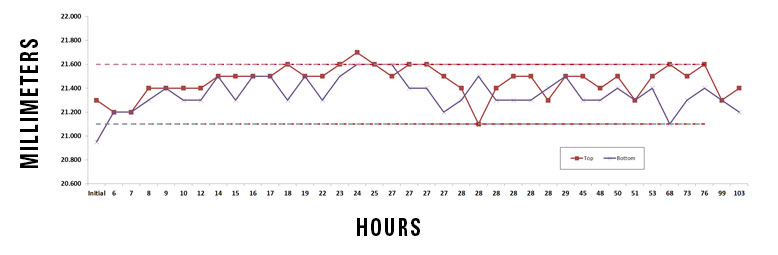
bottom thickness to increase throughout the test. In looking at the graph, this is clearly not the case. The relatively minor variation in thickness is insignificant for most, if not all, industrial applications. Again, when compared to mineral wool’s allowed 5% deviation in thickness when tested for sag-resistance, InsulThin HT comes in considerably below that at + 1.5%.
This test is an example of an environment with excessive vibration, and it represents what can be expected from InsulThin HT in a similar environment in the real world: resistance to vibration resulting in consistent thickness and thermal performance. Because of InsulThin HT’s uniform density and high compressive strength, its structural integrity, and subsequently the thermal performance, will remain intact in high temperature and vibrational applications.
1. ASTM C411 Standard Test Method for Hot-Surface Performance of High-Temperature Thermal Insulation.